Avec sa nouvelle presse à haute fréquence, le Groupe Ducerf accélère sa transformation
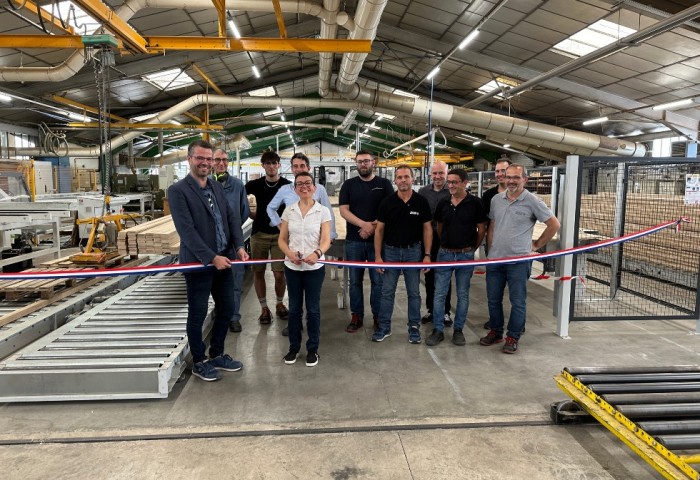
Le Groupe Ducerf a investi 1,7 M€ dans une toute nouvelle presse à haute fréquence. Un équipement ultra-moderne 4 en 1, qui élargit aussi les gammes et les formats de nos produits. Ainsi, nos panneaux massifs Panoplot®, panneaux lamellés-collés Patchwood®, carrelets de menuiserie, ainsi que les premiers éléments de futurs panneaux CLT chêne (cross laminated timber) sont désormais fabriqués sur cette machine signée Weinig. Tout en améliorant significativement la gestion des ressources et l’ergonomie de travail de nos opérateurs !
Depuis l’été 2024, le Groupe Ducerf entre dans une nouvelle ère. Avec l’installation d’une presse à haute fréquence sur le site des Bois Profilés de Charolles (71) pour un investissement de 1,7 million d‘euros, notre entreprise familiale dispose désormais d’une technologie de rupture. « On a fait le constat depuis quelques années que notre frein principal au développement était notre capacité de collage, explique Julien Guenard, responsable du pôle Seconde transformation. Nous arrivions à saturation. Sur certains îlots de production, nous étions en 3 x 8. L’idée de cet investissement, c’est de se donner de la souplesse, d’accroître nos capacités de développement, d’avoir une meilleure qualité de collage. Et enfin, de s’ouvrir de nouveaux horizons. »
Retrouvez notre reportage ici
Car cet investissement revêt pour le groupe bourguignon un intérêt majeur, pour le présent comme pour le futur. « C’était nécessaire si l’on veut continuer à proposer des produits bois d’ingénierie fabriqués en France, indique Thibault Chastagnier, directeur Technique du Groupe Ducerf. Il faut se moderniser, avoir des outils de dernière technologie pour améliorer nos productivités et optimiser le rendement de la matière. Aujourd’hui, nous avons un outil qui permet de fabriquer quatre produits différents sur une même ligne, avec des possibilités de formats différents. Que ce soit pour le carrelet de menuiserie, le panneau massif Panoplot®, le panneau lamellé-collé Patchwood® et pour demain, les plis de notre CLT chêne. Cela va nous permettre de continuer à mettre sur le marché des produits à des prix acceptables, de haute qualité et destiné à la construction. »
« Quatre produits avec des panneaux jusqu’à 6 mètres de long »
Cette machine, co-conçue avec l’entreprise allemande Weinig, mesure 50 mètres de long par 10 mètres de large. En seconde transformation, c’est désormais la ligne de production la plus importante du groupe. Elle remplace trois anciennes presses à froid, et grâce à sa technologie de haute fréquence elle permet d’atteindre des cycles de collage bien plus rapides qu’auparavant. Son principe de fonctionnement ? Faire passer un courant électrique entre le plateau bas et le plateau haut, via le joint de colle qui est essentiellement composé d’eau. Ainsi, le joint de colle monte en température et voit la réticulation de sa colle accélérée. Résultat ? Cela permet de garantir un collage de haute qualité, dans un temps réduit.
De plus, « cette presse nous permet d’étendre l’offre sur le panneau Patchwood, détaille Julien Guenard. Cela répond à un besoin de nos clients, afin de mieux optimiser leurs découpes et donc d’avoir le moins de chutes possible. On va pouvoir produire des panneaux de 6 mètres de long, par 120 cm de large, par 10 cm d’épaisseur. [o1] Pour le Panoplot, c’est essentiellement l’intérêt d’étendre nos gammes de largeurs et de développer la production sur mesure comme nous l’avons fait dernièrement pour notre client Bastiat qui produit les chaises de Notre Dame. Pour la gamme carrelet, nous allons aller deux fois plus vite, ce qui nous offre plus de souplesse et de réactivité pour nos clients. Et enfin, nous sommes, ici en Bourgogne, à l’origine d’un projet de production de murs en CLT chêne et cette presse va nous permettre de fournir des éléments de panneaux en grand format, semi-ouvrés permettant la composition des différents plis du panneau lamellé croisé. »
« Nous limitons fortement le gaspillage de matières »
Derrière cet investissement, c’est la volonté du Groupe Ducerf de maintenir une production française et de soutenir la filière locale de bois qui s’exprime. « Ces derniers temps, nous ressentons un engouement pour les produits bois français, abonde Thibault Chastagnier. Ce sont désormais de véritables politiques d’achats. Cette politique de sourcing national est devenue capitale pour eux, nous le voyons chez nos clients négociants et chez nos industriels. En tant qu’acteur majeur de ce domaine, nous nous devions de suivre ce marché, en investissant de cette manière pour répondre aux enjeux de demain. »
Outre le Made in France, en se donnant la possibilité d’utiliser plus d’essences de bois dans une plus large palette de qualités, le Groupe Ducerf progresse aussi dans sa gestion de la ressource. « Sur cette presse, on va coller des lames de grandes longueurs. Celles-ci sont réalisées à partir d’avivés et de frises aboutées qui sont des produits de scierie. Le bois massif abouté c’est notre savoir-faire, explique Julien Guenard. Aujourd’hui on va pouvoir aller plus loin avec cette presse en valorisant aussi du chêne de qualité secondaire pour la production de panneaux CLT. Ainsi on valorise une ressource qualitative qui est peu ou mal exploitée, parce que trop basse, pour la coller afin de fournir la nouvelle unité de production de produits structurels. » S’ajoute aussi à cela la réduction de consommable comme la colle. « La précision avec laquelle la dépose de colle se fait nous permet de fortement limiter le gaspillage. Le grammage est plus précis et régulier. Et le nettoyage bien moins compliqué. »
« Cela change complètement nos conditions de travail »
C’est là aussi l’un des avantages de cette nouvelle presse. Le travail des opérateurs est considérablement simplifié, comme l’explique Dominique Chapuis, l’un des opérateurs de la nouvelle presse. « Avec cet outil dernière génération, c’est moins de mauvaises postures et moins de pénibilité, puisque l’on travaille toujours à hauteur d’homme. Désormais, nous sommes plus dans l’observation que dans la manipulation. Bien entendu, cela change complètement nos conditions de travail. Plus de mal de dos, moins de fatigue, on rentre à la maison dans un tout autre état. Et puis, il y a la fierté de travailler avec de nouvelles technologies et de pouvoir monter en compétences. » Mentionnons qu’une partie de cet investissement a été soutenu financièrement par la CARSAT BFC dans le cadre d’un contrat de prévention des risques professionnels. Une expérience d’autant plus enrichissante que les opérateurs ont participé au bon déroulement du projet et au développement de l’outil. « C’est un investissement qui a été construit avec les équipes et c’est ce qui rend cet investissement vertueux, insiste Thibault Chastagnier. Dès l’amont du projet, ils ont eu l’occasion d’aller visiter des machines similaires dans d’autres établissements pour nous faire un retour constructif, pour participer à la rédaction des cahiers de charges et donner leurs avis sur le choix du fournisseur retenu. »
En résumé, avec cet investissement conséquent, le Groupe Ducerf pose les bases de son futur, en termes d’humain, de productivité, de créativité et d’écologie. « Cet investissement, c’est la première pierre dans notre projet de réindustrialisation du groupe, ajoute Thibault Chastagnier. Une machine qui faisait du quatre en un dans le collage, cela n’existait pas. C’est le symbole des valeurs du Groupe Ducerf : l’humain au centre, la technologie, l’innovation et le service apporté à nos clients ! »
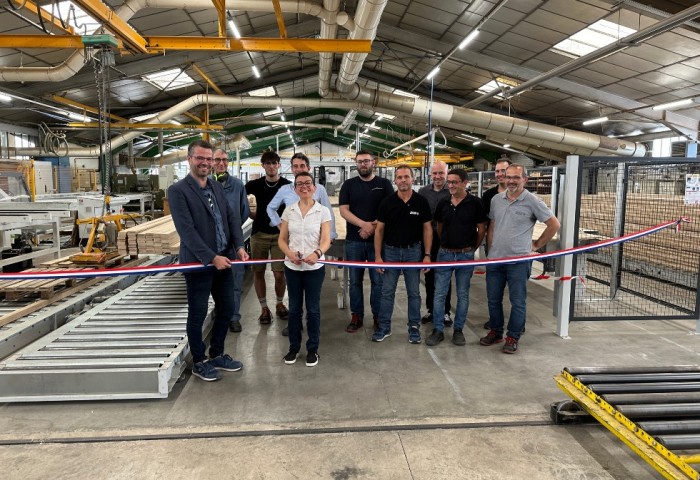